1.搪玻璃设备生产作业程序
图1:搪玻璃设备生产作业程序
2.搪玻璃设备的基材
(1)搪玻璃釉
搪玻璃釉是制造搪玻璃设备的主要原料,搪玻璃釉的制造技术水平及质量对搪玻璃设备的使用寿命有着重要的影响。
1)搪玻璃底釉与金属基体直接结合,要求搪玻璃底釉的膨胀系数与基体相适应、在低温处有理想的密着性、较宽的烧成幅度,以适应多次搪烧、底釉不能有烧焦和产生铜头的现象,同时要求抗鳞爆性强、再沸(暗泡、泡影)倾向低、发泡温度高或不明显等特点。
2)搪玻璃面釉直接与介质接触,因此要具有耐腐蚀、耐温等性能。一般搪玻璃容器带有搅拌操作,故要有较好的耐磨性和弹性。由于搪玻璃面釉是在搪玻璃底釉烧成后,再涂覆在搪玻璃底釉上烧成,为不破坏底釉质量,其烧成温度应略低于底釉,黏度略小于底釉,膨胀系数与底釉匹配,小于金属基体。为使表面美观有光泽,色彩须均匀稳定。
使用优质搪玻璃釉生产的搪玻璃设备瓷层能降低瓷层的气孔率、提高瓷层的有效厚度、提高瓷层的密着性、降低瓷层的残余应力、提高瓷层的耐腐蚀能力和耐冷热冲击性能。具体的搪玻璃釉配方应根据搪玻璃制造企业的生产条件、制造工艺、钢板材质以及化工企业具体搪玻璃设备内的温度、压力、介质的腐蚀性决定,以达到用户的工艺和使用年限要求。
(2)钢材
大量用于制造搪玻璃制品的基体材料主要是优质低碳钢、铸铁和不锈钢,其中以低碳钢及铸铁最为普遍。前者作为搪玻璃的适用钢,大量用来制作设备和容器;后者由于能浇铸成型复杂部件,且成本低廉,被广泛用以制造泵、阀、小型设备及零配件。作为搪玻璃设备的专用钢材,主要考虑的应用性能有以下几个方面:
一是力学性能,二是作为压力容器材料的韧性要求,三是保障冷加工成型性能,四是搪瓷性能。
影响搪玻璃钢材应用性能的化学元素主要有C、Mn、Si、P、S以及添加的合金元素Ti、Ni等,具体元素的作用如下:
1) C含量的影响最大,一般要求<0.19%,搪玻璃钢材一般碳含量为0.12%~0.19%。碳含量低,可增加钢材的韧性和可塑性,提高钢材的冷冲压、焊接等成型性能,提高可搪性。碳含量高,成型性能较差。同时会使瓷层表面产生针孔、鼓泡以及鱼鳞状脱落。
2) Mn能提高钢的韧性,使钢板具有良好的冲压性能,同时,Mn能与S生成MnS在搪烧温度下性能稳定,有利于消除有害的SO2气体。
3) Si能提高钢的强度、调节膨胀系数,但会降低钢的韧性和延展性,过高的Si含量会使搪玻璃釉与钢材的密着性降低。因此,应控制在一定的范围,一般Si含量≤0.15~0.5%。
4) P和S都是有害元素,会增加钢的脆性,不利于机械加工,同时会形成对搪玻璃层密着性不利的SO2气体。P和S含量过高极易形成偏析,夹杂增多,一般P应控制在<0.03%,S应控制在<0.02%。
5)钛是个活泼元素,具有脱氢作用,又能与碳、硫、氮等元素生成化合物,能控制鳞爆的产生,一般加入量应控制在Ti/C(质量比)为4~8。
为了保障钢材的强度,确定适当的碳含量、控制适当含量的Mn以提高钢材固溶强化的幅度。提高钢材的韧性水平,主要是通过控制钢的沉淀强化幅度适中,控制尽可能少的珠光体并控制钢的晶粒适度细化,同时考虑控制MnS等夹杂物的形态和分布来保障,这也同时保障了钢的冷成型性能。搪瓷性能是该钢种必须考虑的重要问题,包括抗气孔性能、抗鳞爆性能以及密着性能。
提高钢材的抗气孔性能和抗鳞爆性能需要降低钢材中的C、S、P、Mn含量,适当加入一定量的Ti。降低钢材中C、S、P的含量,高温搪烧时产生的CO、CO2、S O2、P2O5气体就少,Ti会在高温时与C生成TiC,大量地减少了搪烧时金属与非金属界面上生成的CO、CO2气体,同时TiC还能捕捉渗入钢材中氢原子,使钢材内空穴及界面生成氢气的几率降低,随着钢材空穴中氢气的减少,钢材抗鳞爆性能也就提高了。另外钢中的Mn、S的含量超过一定值时,其透水性也急剧增加,高温搪烧时产生的氢增多,瓷层鳞爆的几率也相应增加。钢板与瓷釉是通过密着层结合的,密着层是搪玻璃釉与钢的一种氧化物结合层。影响密着性的原因有很多,搪玻璃釉与钢板的浸润性是一个主要方面,钢中Si等元素的含量也是一个重要原因,钢材中的Si在搪烧过程中会先行生成氧化物膜,阻碍密着层的生成,为此在设计中,对钢材中Si含量应进行严格的限定。
3.底胎的要求
搪玻璃设备的质量,首先决定于铁胎,没有高质量的铁胎,就不可能有高质量的搪玻璃设备。要保证制品质量,铁胎应满足以下六条要求:
(1)铁胎表面应平整,不得有显著的工具伤痕、凹坑、夹层等机械缺陷;
(2)铁胎表面的焊道要平直、规整,焊缝宽度不得超过钢板厚度的1.5倍。焊缝接头要圆滑地过渡,不允许有夹渣、气孔、咬边、未焊透等缺陷;
(3)铁胎表面的焊缝在喷砂前要进行磨光;
(4)铁胎表面的对接焊缝错边量要小于厚度的10%且不大于3mm;
(5)法兰不平度要小于直径的0.15%;
(6)对接法兰的压紧面要保证设计压力下的密封。
4.表面处理
铁胎加工好后,由于基材表面质量往往达不到搪瓷的工艺要求,如金属表面尚有氧化层、表面夹皮(轧制时造成)、焊缝缺陷及机加工过程中粘附的油脂污物等,都要影响搪烧质量,因此必须进行磨光、烧油脱碳和喷砂等表面处理。
磨光一般在砂轮机上或用手提砂轮进行。磨光的要求是将搪烧面上焊缝磨平、将尖棱角磨圆、将氧化皮及夹皮磨去,现出金属本色。
烧油脱碳是将粘附的油脂、有机物等在高温下烧除。有时钢板含碳量超过标准规定时,也采取高温表面脱碳的办法来作补偿处理。
搪玻璃设备损坏后到制造厂进行复搪,必须进行热处理(脱氢),以消除爆瓷部位基材渗入的氢。
喷砂是将铁胎表面打粗糙,增加表面自由能及比表面积,从而提高底胎金属与底釉的密着。
5.修胎
经过表面处理后的铁胎,在正式喷搪瓷釉前,要细致地检查,凡是不符合搪瓷工艺要求的“毛病”均应及时处理,如毛刺、尖锐角、凹凸坑、夹层、沙眼等,这些“毛病”可采用手工打磨,挖铲补焊再磨平等作业修磨。
6.搪烧底釉
铁胎修磨好以后即可进行喷涂和搪烧底釉。喷涂的方式为手工和机械化(半自动)喷涂,由于喷枪口径、喷涂用空气压力及釉浆稠度间是相互关联的,两种喷涂方式所使用的釉浆稠度控制不一样,需要根据操作人员的经验自己掌握。喷搪底釉的要点是要使头遍底釉厚薄均匀,其厚度值控制在烧成后为200±50μm合适。底釉喷涂于铁胎后要经过干燥,一般采取自然干燥、放到烘房内干燥、放在炉前或出炉的制件边进行缓慢的烘烤,要注意防止快速烘烤,快速烘烤易使粉层开裂。粉层干燥后即可进烧成炉内进行烧成,底釉的烧成温度应不高于底釉的熔点,底釉的烧成必须精心掌握温度、时间,即不能烧成不足(俗称烧得生)也不能火大(俗称烧过),前者密着不好,后者会烧损底釉。烧成适度的底釉应该是色泽均匀、表面平滑光亮、无气泡。头遍底釉烧好后,质量合格即可进行喷搪面釉,质量不合格需要修磨,烧损严重时需要喷搪第二遍底釉,两遍底釉的总厚度控制在350μm以下,过厚就会影响面釉层的有效厚度。
7.搪烧面釉
搪玻璃设备瓷层真正起到防腐作用的是面釉层。底釉搪烧好后,质量符合要求即可进行面釉喷涂和搪烧,面釉层喷涂和搪烧的工艺要求除去面釉搪烧温度低于底釉搪烧温度外与底釉相似。面釉层的厚度,一般要求1mm左右,具体根据使用要求而定,如考虑传热应使瓷釉层薄些,不需传热而使用的介质腐蚀性严重时瓷釉层可厚些。国外允许最厚达2.55mm,我国标准则规定0.8-2.0mm,公称容积大于或者等于10000L时,厚度上限可允许至2.2mm,公称容积大于或等于20000L时,厚度上限可允许至2.4mm。要达到规定瓷厚,产品上的面釉要喷搪多遍,每遍厚度以薄一些为好,但考虑生产效率,也不能太薄,一般以控制每遍厚度增加0.2mm为佳。如果金属表面状况好,焊缝不出问题,喷搪过程中修磨细致,那么喷搪三遍到四遍面釉后就可达到规定厚度。为保证搪烧质量,每喷搪一遍,都要经过检查,检查瓷面上是否有暗泡、针孔等,一经查到就应打磨开进行修补。对于直通金属表面的针孔和暗泡要磨挖,甚至补焊,凡见金属的修补处,必须补喷底釉。
8.优质搪烧
目前,比较先进的搪烧技术是使用具有可控温技术电炉,采用的“常温进入”、“低温长烧”以及“搪烧后缓冷”烧成工艺烧制搪玻璃设备,可控温电炉要求炉内各部位的温度能控制在上下10℃以内。 “常温进入”是讲喷完瓷釉的设备在常温时进入烧成炉,缓慢均匀升温,这样设备各个部位受热均匀、升温一致,设备釜体各部位因升温不一致产生的应力就小。“低温长烧”的“低温”是讲的通过合理配比把瓷釉的熔点降低100℃甚至更多,随着瓷釉熔点的降低胎体的变形量随之变小、烧成时胎体的最高温度也相应降低,最终减少了设备的变形公差和胎体在更高温度时吸收的氢气。“低温长烧”的“长烧”是讲在瓷釉的熔点保温一段时间,瓷釉与瓷釉、瓷釉与胎体最大程度相互混熔、互渗,瓷釉在熔融时产生的气体以及瓷层与钢板界面产生的一氧化碳和二氧化碳充分释放,以提高胎体瓷层的结合强度、降低瓷层的气孔率提高瓷层的密实度和瓷层的有效厚度。“搪烧后缓冷”是讲在瓷层、胎体的最佳应力释放温度段和释放胎体内氢气最佳释放温度段分别保温一段时间,使瓷层、钢板的张应力、压应力以及钢板中的氢气尽可能得到释放。用可控温烧成炉依照比较先进的烧成工艺烧制的搪玻璃设备瓷层不会出现烧的生、烧过现象,瓷层密实度高有效厚度大、层与层之间融合好结合强度高、瓷层耐腐蚀性优良。
9.搪玻璃件成品质量及技术指标
9.1搪玻璃层表面质量
1)在距搪玻璃层表面250mm处,用36V、60W手灯,目测搪玻璃层表面,不应有下列缺陷:
①裂纹、鱼鳞爆、局部剥落;
②暗泡、粉瘤:暗泡、粉瘤部位经机械处理后表面平滑、平整,且经直流高压电检测通过,搪玻璃厚度符合9(3)1)的要求,则判定此部位质量合格;
③明显的擦伤;
④由烧成托架引起妨碍设备使用的局部变形;
⑤影响设备正常使用的发纹。
2)每平方米搪玻璃层上的杂粒不得超过三处,每处面积不应大于4mm。
允许采用机械手段清除搪玻璃层浅表面的异物,清除部位搪玻璃层厚度和高压电试验应符合9(3)1)、9(3)2)的要求。
3)搪玻璃层表面允许有色泽差异,但制造厂应保证色泽差异部位的性能符合标准,且不影响设备的正常使用。
9.2搪玻璃件的形位公差
搪玻璃部件、塔节、管道及管件的形位公差按HG/T2637检测,其结果应符合表2、表3的规定。设计压力超出表1的搪玻璃设备搪玻璃件的形位公差由供需双方约定。
表1:搪玻璃件的位型公差
表2:搪玻璃塔节及管道、管件的形位公差
塔节
|
公称直径DN
|
300~1000
|
1100~1600
|
塔节法兰对塔节轴线的垂直度c
|
≤3.5
|
≤4.5
|
管道、管件
|
公称直径DN
|
25~80
|
100~150
|
200~250
|
管法兰对管法兰的垂直度、平行度、倾斜度
|
≤1
|
≤2
|
≤3
|
塔节、管道直线度c
|
≤0.3%L
|
注:L为塔节高度或管道的长度,c为公差值(见图3)
|
图3:搪玻璃塔节及管道、管件的形位公差示意图
3)搪玻璃设备耐温差急变性
搪玻璃设备的耐温差急变性是指搪玻璃面或其反侧的金属基体经受突然温度急变的性能。
搪玻璃设备耐温差急变温度为:冷急变温度为110℃,热急变温度为120℃。
搪玻璃设备的耐热差急变性请按下面进行检测:
室温条件下向设备夹套内充满洁净水,使夹套温度到水的温度,保持20min后,测量搪玻璃层表面温度,加热导热油的温度为120℃±3℃加搪玻璃层温度。自下而上向设备各部位搪玻璃面层表面迅速泼热油,每次泼油量为0.5L,隔5min泼一次,泼油部位和点数如下:
下液口部位3次;
下接环部位5次;
下环焊缝部位10次;
直筒体部位10次
上接环部位10次;
高颈法兰部位10次。
(4)针孔
1)搪玻璃层有效工作面若出现针孔,允许用钽材加聚四氟乙烯材料修复。修复部位应不影响设备的正常使用。修补材料供需双方也可在合同中另行约定。
2)搪玻璃设备搪玻璃层针孔修补数目不得超过表3
表3:搪玻璃设备针孔修补数目
公称容积/kL
|
搪玻璃面有效面积(参考)/m²
|
针孔修补数
|
≤8
>8~12
>12~15
>15~20
>20~30
>30~40
>40~60
>60
|
≤24
>24~31
>31~35
>35~45
>45~55
>55~67
>67~89
>89
|
0
1
2
3
4
5
6
7
|
9.4.3搪玻璃塔节针孔修补数目不得超过表4:
表4:搪玻璃塔节针孔修补数目
塔节公称直径
|
塔节长度/mm
|
<3000
|
≥3000
|
<800
|
0
|
0
|
800≤DN<1300
|
0
|
1
|
≥1300
|
1
|
2
|
4)密封面以及影响设备操作的部位不允许钽钉修补。
(5)搪玻璃设备配套件
搪玻璃设备配套件,如卡子、活套法兰、垫片、温度计夹套、搅拌器、填料箱、放料阀、机械密封、减速机、视镜玻璃等,应符合本标准和相关标准的要求。
(6)特殊约定
当供需双方在合同中根据使用的特殊要求对搪玻璃质量另有约定时可不按上述要求执行。
10.出厂前检验
由于搪玻璃设备多数用于苛刻的腐蚀环境中,因此对制品的质量检查要十分严格。检查检验要求要根据制品本身的等级要求按照以下内容进行,产品经检验合格即可组装或包装出厂。需要组装的制件,在组装后还要进行检验,只有整个制件合格后才算合格品、才能包装入库,销售前设备应静置半月以上以消除残存应力。
(1)表面质量
对搪玻璃件搪玻璃层的表面质量,按9(1)中规定逐条检验。
(2)形位公差和物理机械性能
对搪玻璃件的型位公差、搪玻璃层的厚度及耐直流高电压性能,请按9(2)(3)的规定逐件进行检验。
(3)液压试验
1)搪玻璃设备内容器和夹套的液压试验压力按表5规定。内容器液压试验可选择表5中的任一种方式。液压试验方法按GB/T7994进行。
2)搪玻璃塔设备的耐压试验压力、试验方法应按图样规定。搪玻璃塔节在出厂前可不进行耐压试验(如带夹套应按10(3)1)条中进行试验),但应在现场组装后进行耐压试验。
3)搪玻璃真空设备液压试验压力按表5规定。
表5:搪玻璃设备液压试验
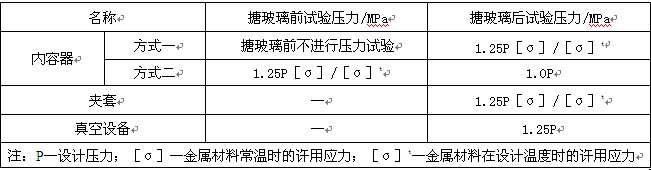
(4)气密性试验
1)盛装介质毒性为极度、高度危害和设计上不允许有微量泄露的搪玻璃压力容器,设备组装好后应依次进行液压试验和气密性试验。如设备在制造厂组装液压试验合格,在用户现场安装好后,投产前应经气密性试验合格。
2)设备气密性试验方法按照GB/T7995的规定进行。对承压设备,试验压力为1.0倍的设计压力;对真空设备,试验压力为0.1MPa,气密性试验结果应无泄漏。
(5)直流高压电检测
经过耐压试验后,应对用于强腐蚀性介质的设备进行10kV直流高压电检测并通过;用于弱腐蚀性介质的设备进行5kV直流高压电检测并通过。
(6)设备耐温差急变性试验
搪玻璃设备的耐温差急变试验不作为常规检验项目,但是在下列情况下应进行设备的耐温差急变性试验:
1)搪烧工艺发生重大调整时;
2)使用新烧成炉或烧成炉发生重大改造时;
3)搪玻璃釉配方发生重大调整或搪玻璃釉供应商改变时;
4)用户提出要求时。
以上1)、2)、3)三种情况发生时,制造厂应尽可能选择大公称容积的设备进行耐温差急变性试验。
(7)高电压复验
如用户在合同中有复验条款时,则进行用户复验。复验时应有制造单位人员参加。设备进行直流高电压试验的复验电压,对强腐蚀性介质的设备为7kV,对弱腐蚀性介质的设备为3kV。仲裁检验或第三方检验时,对强腐蚀性介质的设备直接高电压试验的电压为10kV,对弱腐蚀性介质的设备为3kV。
|